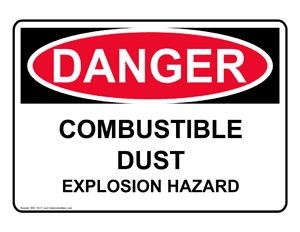
What is Dust Hazard Analysis (DHA)?
DHA is a systematic review to identify and evaluate potential fire, flash fire, and explosion hazards associated with the presence of combustible particulate solid(s) in a process or facility.
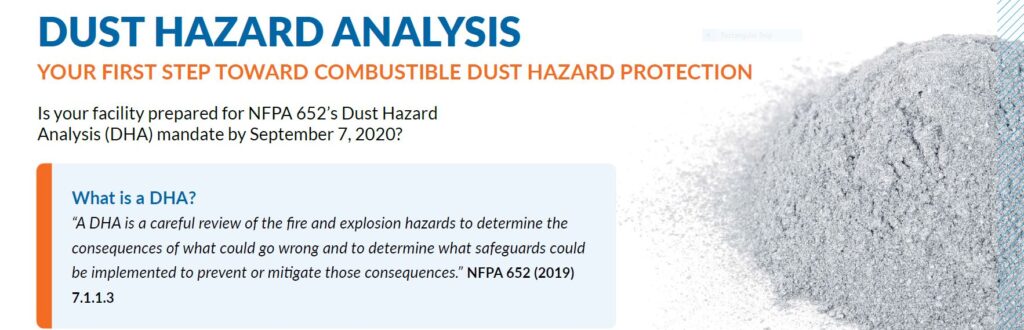
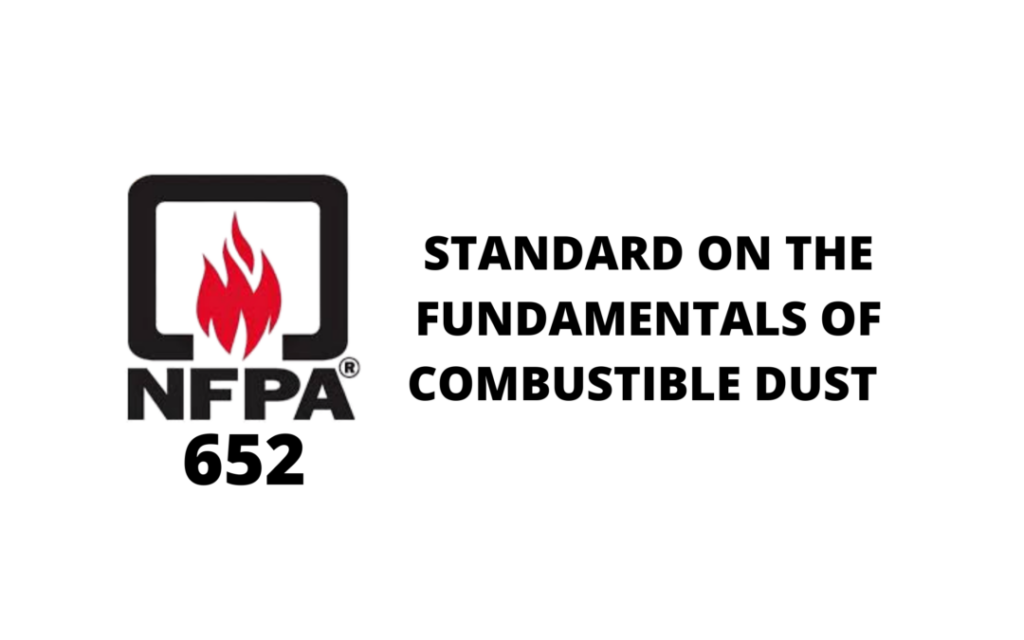
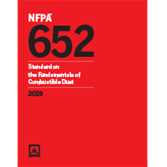
Who is required to complete a Dust Hazard Analysis?
NFPA 652-1.3.2 This standard shall apply to all facilities and operations that manufacture, process, blend, convey, repackage, generate, or handle combustible dusts or combustible particulate solids.”
Who can complete a DHA
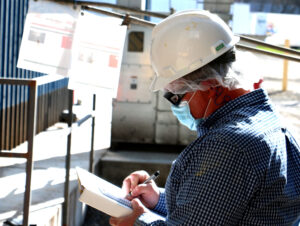
NFPA 652-7.2.2 requires that the “DHA shall be performed or led by a qualified person.”
NFPA 652-3.3.39 defines a qualified person as “a person who, by possession of a recognized degree, certificate, professional standing, or skill, and who, by knowledge, training and experience, has demonstrated the ability to deal with problems related to the subject matter, the work, or the project.”
How to prepare for a DHA?
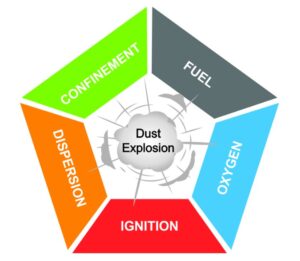
Identify and inform your team leads, such as engineers, operators and maintenance technicians of the upcoming DHA so they can provide valuable information about the production process. Collect important documents such as facility layout drawings, process flow diagrams, OEM cut sheets, incident logs
and more, all of which will help the DHA specialist not only determine which areas could be hazardous but also which are safe and may be ignored.
Documenting the various types of materials handled, conveyed and stored throughout the process and their locations. Any unique mixtures should also be noted, as those may require dust testing if their explosibility values are unknown.
What to expect during a DHA walk through
The production process may or may not need to be stopped for the DHA to be conducted. In fact, the DHA specialist will likely want to analyze it while running, so they can have a proper understanding of the operation. However, there may be exceptions if process startup or shutdown create unique hazards that require analysis.
Inspect equipment for dust hazards by evaluating if the material is being handled in a way that can create a dust cloud in the equipment. This means understanding the particle sizes involved as well as the way the material is manipulated. It’s important to consider normal operations, start-up and shutdown, and potential upset conditions. The facility’s team leads will be critical in providing valuable institutional knowledge of the equipment.
Identify potential ignition sources which may ignite a dust cloud, and determine preventative measures to reduce the risk of these ignition sources from ever occurring. Possible ignition sources include open flames, overheated surfaces, sparks, foreign objects from connected equipment, electrostatic discharges, and more.
Review existing safeguards, such as explosion vents, suppression systems, isolation systems, fire suppression systems, rotary valves and more to ensure they are being used properly and remain compliant with the latest codes and testing standards. Inspect rooms and buildings for external hazards where dust may accumulate outside of the process, including on the ground, on overhead surfaces, on light fixtures and more. History has proven that some of the most devastating combustible dust explosions have occurred in part because of these secondary explosion hazards.
How often are dust hazard analysis required?
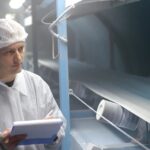
NFPA 652-7.1.4 states a DHA shall be reviewed and updated at least every 5 years.” Also, any equipment additions or process modifications are required to be reviewed through a DHA.
Why choose Fike/SSI for your DHA?
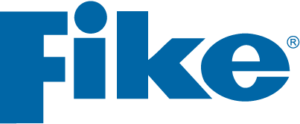
SSI is a wholly owned subsidiary of Fike Corporation. Fike’s unmatched experience and equipment helps to protect industrial processes around the world from explosions, fires, and pressure-related hazards to safeguard critical assets and business continuity. Once Fike completes your DHA, SSI can then work with you to develop and implement a comprehensive protection strategy that may include some or all of our capabilities:
/ Protection System Design
/ Full Portfolio of Explosion Protection Products
/ Installation and Commissioning
/ Ongoing Service and Maintenance
/ Full-Scale Testing Capabilities
/ Phased Implementation Strategy – Work within your budgeting constraints and mitigation strategies
/ Meet current NFPA combustible dust standards and work with local AHJ to meet OSHA, Fire Marshall, and site specific insurance requirements
Dust Collector Fire Suppression Systems Information
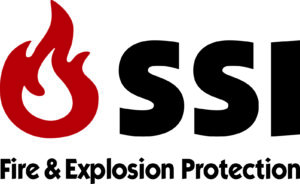
Explosion protection is important to your business. Finding the solutions to your explosion protection needs is something we have been doing since 2004. Our customers have found that they can trust the experience, knowledge, honesty, integrity and ethics of SSI’s sales team. We invite you to contact one of the members of this team to discuss how SSI can protect your employee’s life safety and your valuable assets for the continued operation and success of your company. Contact us or call 1-800-360-0687 for a System Sales and Design Consultant to perform a needs analysis at your facility.
You must be logged in to post a comment.